Continuous distillation: Difference between revisions
imported>Milton Beychok m (Wiki links) |
mNo edit summary |
||
(3 intermediate revisions by 2 users not shown) | |||
Line 49: | Line 49: | ||
The first vertical continuous distillation column, used in alcohol distilleries and known as the ''patent still'', was developed in 1813 and patented by a [[France|Frenchman]], Jean-Baptiste Cellier Blumenthal. In 1822, Anthony Perrier of [[England]] developed an early version of the bubble-cap tray. Packing media (2-3 cm glass balls) had already been used by Nicolas Clement of France in an alcohol still referred to as a ''colonne absorbante'' and ''cascade chimique''. | The first vertical continuous distillation column, used in alcohol distilleries and known as the ''patent still'', was developed in 1813 and patented by a [[France|Frenchman]], Jean-Baptiste Cellier Blumenthal. In 1822, Anthony Perrier of [[England]] developed an early version of the bubble-cap tray. Packing media (2-3 cm glass balls) had already been used by Nicolas Clement of France in an alcohol still referred to as a ''colonne absorbante'' and ''cascade chimique''. | ||
In 1831, after a career as an excise inspector in [[Scotland]], Aneas Coffey (born in France and educated in | In 1831, after a career as an excise inspector in [[Scotland]], Aneas Coffey (born in France and educated in Ireland) developed the first sieve tray column known as the ''Coffey still'' which was subsequently used quite widely in Scottish whiskey distilleries. | ||
The first book on the fundamentals of distillation, ''La Rectification de l'alcool'' was written by Ernest Sorel in 1893. | The first book on the fundamentals of distillation, ''La Rectification de l'alcool'' was written by Ernest Sorel in 1893. | ||
Line 109: | Line 109: | ||
=== Continuous distillation of crude oil === | === Continuous distillation of crude oil === | ||
[[Petroleum]] crude oils contain many hundreds of different [[hydrocarbon]] compounds: [[paraffin]]s, [[naphthene]]s and [[aromatic]]s as well as [[Organic chemistry|organic]] [[ | [[Petroleum]] crude oils contain many hundreds of different [[hydrocarbon]] compounds: [[paraffin]]s, [[naphthene]]s and [[aromatic]]s as well as [[Organic chemistry|organic]] [[sulphur]] and [[nitrogen]] compounds and some [[oxygen]] containing hydrocarbons such as [[phenols]]. Although crude oils generally do not contain [[olefin]]s, they are formed in many of the processes used in a petroleum refinery.<ref name=Gary>{{cite book|author=Gary, J.H. and Handwerk, G.E.|title=Petroleum Refining Technology and Economics|edition=2nd Edition|publisher=Marcel Dekker, Inc.|year=1984|id=ISBN 0-8247-7150-8}}</ref> | ||
The continuous distillation of petroleum crude oil (commonly referred to as ''crude oil fractionation'') is the first processing unit in virtually all petroleum refineries worldwide. It is a somewhat unique example of distillation because it does not produce products having a single boiling point. Instead, it produces ''fractions'' having ''boiling ranges''.<ref name=Gary/><ref>{{cite book|author=Nelson, W.L.|title=Petroleum Refinery Engineering|edition=4th Edition|publisher=McGraw Hill|year=1958|id=LCCN 57010913}}</ref> | The continuous distillation of petroleum crude oil (commonly referred to as ''crude oil fractionation'') is the first processing unit in virtually all petroleum refineries worldwide. It is a somewhat unique example of distillation because it does not produce products having a single boiling point. Instead, it produces ''fractions'' having ''boiling ranges''.<ref name=Gary/><ref>{{cite book|author=Nelson, W.L.|title=Petroleum Refinery Engineering|edition=4th Edition|publisher=McGraw Hill|year=1958|id=LCCN 57010913}}</ref> | ||
Line 115: | Line 115: | ||
[[Image:Crude Distillation 2.png|center|thumb|461px|{{#ifexist:Template:Crude Distillation 2.png/credit|{{Crude Distillation 2.png/credit}}<br/>|}}Figure 4: Schematic diagram of a crude oil fractionator.]] | [[Image:Crude Distillation 2.png|center|thumb|461px|{{#ifexist:Template:Crude Distillation 2.png/credit|{{Crude Distillation 2.png/credit}}<br/>|}}Figure 4: Schematic diagram of a crude oil fractionator.]] | ||
For example, a crude oil fractionator produces an overhead fraction called ''[[Petroleum naphtha|naphtha]]'' which becomes a [[gasoline]] component after it is further processed through a catalytic [[Hydrodesulfurization|hydrodesulfurizer]] to remove [[ | For example, a crude oil fractionator produces an overhead fraction called ''[[Petroleum naphtha|naphtha]]'' which becomes a [[gasoline]] component after it is further processed through a catalytic [[Hydrodesulfurization|hydrodesulfurizer]] to remove [[sulphur]] and a [[Catalytic reforming|catalytic reformer]] to reform its hydrocarbon [[molecule]]s into more complex molecules with a higher [[octane rating]] value. | ||
The ''naphtha cut'', as that fraction is called, contains many different hydrocarbon compounds. Therefore it has an initial boiling point of about 35 °C and a final boiling point of about 200 °C. Each cut produced in the crude oil fractionator has a different boiling range. | The ''naphtha cut'', as that fraction is called, contains many different hydrocarbon compounds. Therefore it has an initial boiling point of about 35 °C and a final boiling point of about 200 °C. Each cut produced in the crude oil fractionator has a different boiling range. | ||
Line 121: | Line 121: | ||
At some distance below the overhead, the next cut is withdrawn from the side of the column and it is usually the ''[[jet fuel]] cut'', also known as a ''[[kerosene]] cut''. The boiling range of that cut is from an initial boiling point of about 150 °C to a final boiling point of about 270 °C, and it also contains many different hydrocarbons. | At some distance below the overhead, the next cut is withdrawn from the side of the column and it is usually the ''[[jet fuel]] cut'', also known as a ''[[kerosene]] cut''. The boiling range of that cut is from an initial boiling point of about 150 °C to a final boiling point of about 270 °C, and it also contains many different hydrocarbons. | ||
The next cut further down the tower is the [[diesel oil]] cut with a boiling range from about 180 °C to about 315 °C (not shown in Figure 4 for reasons of brevity). The next cuts down the tower are the light and heavy fuel oil cuts and finally the bottoms product. | The next cut further down the tower is the [[diesel oil]] cut with a boiling range from about 180 °C to about 315 °C (not shown in Figure 4 for reasons of brevity). The next cuts down the tower are the light and heavy [[fuel oil]] cuts and finally the bottoms product. | ||
The boiling ranges of any two successive cuts overlap because the distillation separations are not perfectly sharp. Typically, all of the cuts from a crude oil fractionator in a petroleum refinery are processed further in subsequent refining processes. | The boiling ranges of any two successive cuts overlap because the distillation separations are not perfectly sharp. Typically, all of the cuts from a crude oil fractionator in a petroleum refinery are processed further in subsequent refining processes. | ||
== References == | == References == | ||
{{reflist}} | {{reflist}}[[Category:Suggestion Bot Tag]] |
Latest revision as of 16:00, 1 August 2024

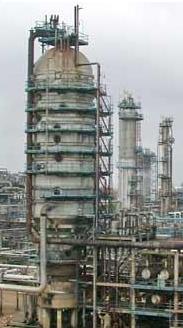
A vacuum distillation column in a petroleum refinery.
Continuous distillation is an ongoing separation process in which a liquid mixture of two or more miscible components is continuously fed into the process and physically separated into two or more products by preferentially boiling the more volatile (i.e., lower boiling point) components out of the mixture.[1][2][3][4]
Large-scale, continuous distillation is very commonly used in the chemical process industries where large quantities of liquids have to be distilled, as in petroleum refining, natural gas processing, petrochemical production, hydrocarbon solvents production, coal tar processing, the liquefaction of gases such as hydrogen, oxygen, nitrogen, and helium), and other low-temperature processing.
Industrial distillation is typically performed in large, vertical cylindrical columns (see the adjacent photographs) commonly referred to as distillation columns, distillation towers or fractionators with diameters ranging from about 65 centimetres to 11 metres and heights ranging from about 6 metres to 60 metres or more.
To provide for the intimate mixing of the upward flowing vapor and downward flowing liquid in distillation columns, the columns usually contain a series of horizontal distillation trays or plates (see Figure 3). The distillation trays or plates are typically separated by about 45 to 75 centimetres of vertical distance. However, some columns are designed to use beds of packing media rather than trays or plates.
Distillation is one of the fundamental unit operations of chemical engineering. If the feed contains more than two components, it is commonly referred to as multi-component distillation and, if it contains only two components, it is referred to as binary distillation.
If the distillation column feed contains a very great number of components (such as is the case in distilling petroleum crude oil), separation into pure components is impractical and such columns are therefore designed to yield fractions which are groups of components within a desired range of boiling points. Those fractions are probably the origin of the terms fractional distillation and fractionation.
There are a number of other forms of distillation such as vacuum distillation, batch distillation, steam distillation, extractive distillation and azeotropic distillation which are not included in this article.
The process
When a liquid mixture is heated so that it boils, the evolved vapor will have a higher concentration of the more volatile (i.e., lower boiling point) components than the liquid mixture from which it evolved. Conversely, when a vapor mixture is cooled, the less volatile components tend to condense in a greater proportion than the more volatile components.
Figure 1 schematically illustrates what happens in a distillation column. A liquid mixture is fed into the distillation column. On entering the column, the heated feed is partially vaporized and rises up the column. However, as it rises, it cools by contacting the descending cooler liquid and partially condenses so that, while part of vapor continues to flow upward, the condensed portion is enriched in the less volatile component(s) and flows downward. As the vapor continues to flow upward, it undergoes partial condensation a number of times and each time becomes richer in the more volatile component(s).
The part of the feed liquid that did not vaporize on entering the column, flows downward and is heated by contacting the upward flowing hot vapor until it is partially vaporized. The resulting vapor flows upward and the residual liquid is enriched in the less volatile component(s) and flows downward. As the liquid continues to flow downward, it undergoes partial vaporization a number of times and each time becomes richer in the less volatile component(s).
The distillation trays in the column are designed to facilitate the intimate contacting of upward flowing vapor with downward flowing liquid (see Figure 3).
The overhead vapor that exits the top of the column is rich in the more volatile component(s) of the column feed and the bottoms liquid which exits the bottom of the column is rich in the less volatile component(s) of the column feed.
(Note: In distillation terminology, when a liquid or vapor mixture attains a higher concentration of some component, it is referred to as being enriched, rich or richer in that component. Also, the more volatile components are called the lighter components and the less volatile components are called the heavier components.)
Heat is required to provide the multiple occurrences of partial vaporization in a distillation column. The required heat is applied to the bottom of a distillation column in a number of ways, the most common being the transfer of heat from a reboiler.
Similarly, cooling is required to provide the multiple occurrences of partial condensation that also occur in a distillation column. The required cooling is most usually provided by a condenser used to cool and condense the overhead vapor into a liquid and then returning part of the cool condensed liquid to the top of the column as reflux.
The overhead condenser may be water-cooled or air-cooled. The bottoms reboiler may be a heat exchanger heated by steam or hot oil, or it might be a fuel-fired furnace. The location of the feed entry can vary from one design to another and is selected to provide optimum results (see McCabe-Thiele method).
A continuous distillation column is kept in a steady state or approximate steady state. In the context of continuous distillation, that means that the feed rate, output product rates, reflux rate, heating and cooling rates, temperatures, pressures, and compositions at every point within the column are essentially kept constant during operation. It also means that the column is material-balanced and heat-balanced (i.e., the material inputs equal the material outputs, and the heat inputs equal the heat outputs). If a variation in conditions does occur, modern process control equipment is usually able to gradually return the system to a steady state again.
Brief history
Distillation is an ancient art which has been practiced for thousands of years, very often for the concentration of the alcoholic content of beverages.[1][5]
The first vertical continuous distillation column, used in alcohol distilleries and known as the patent still, was developed in 1813 and patented by a Frenchman, Jean-Baptiste Cellier Blumenthal. In 1822, Anthony Perrier of England developed an early version of the bubble-cap tray. Packing media (2-3 cm glass balls) had already been used by Nicolas Clement of France in an alcohol still referred to as a colonne absorbante and cascade chimique.
In 1831, after a career as an excise inspector in Scotland, Aneas Coffey (born in France and educated in Ireland) developed the first sieve tray column known as the Coffey still which was subsequently used quite widely in Scottish whiskey distilleries.
The first book on the fundamentals of distillation, La Rectification de l'alcool was written by Ernest Sorel in 1893.
During the first quarter of the twentieth century, the use of continuous distillation expanded from alcohol distilleries to become an important separation process in the chemical industry. Once it was recognized as an effective method for separating petroleum crude oil into useful products, the use of continuous distillation was further accelerated.
Design and operation
The design of a distillation column depends upon the composition and the thermal condition of the feed as well as the composition of the desired products. The McCabe-Thiele method and the Fenske equation may be used to design a simple binary distillation column (as in Figure 1).
To design a column for the distillation of a multi-component feed to provide more than two product distillates (as in Figure 2), computerized simulation models may be used for the design as well as for the subsequent online operation of the column.
Computerized simulation models are also used to determine whether it is possible to adjust the operation of existing columns for the distillation of feed compositions that are somewhat different than the feed composition for which the column was originally designed.
Many industrial uses of continuous distillation operate 24 hours per day for as long as 2-5 years between routine, scheduled maintenance shutdowns. The operational control of a distillation column may be performed by advanced computer control systems but highly experienced workers are still required to oversee the online, real time operations and to provide daily routine maintenance as needed.
Column feed
The manner of feeding a continuous column depends upon the column pressure and the pressure of the feed source. If the feed is from a source at a pressure sufficiently higher than the column pressure, it may be simply piped into the column at the designated feed entry point. A liquid feed from a source at a lower pressure than the column needs to be pumped into the column, and a gas feed from a source at a lower pressure than the column needs to be compressed to a higher pressure before entering the column.
The feed may be a superheated vapor, a saturated vapor, a partially vaporized liquid-vapor mixture, a saturated liquid or a sub-cooled liquid. If the feed is a saturated liquid at a higher pressure than the column pressure and flows through a valve just before entering the column, it will undergo a flash vaporization (also known as an equilibrium flash or a throttling expansion) resulting a liquid-vapor mixture as it enters the column.
Overhead system
Figures 1 and 2 are based on the assumption that the overhead vapor from a distillation column is cooled and totally condensed in a water or air-cooled condenser. However, in many cases, the tower overhead can not be totally condensed with a typical air or water-cooled condenser and therefore the reflux drum must include a gas vent for the uncondensed vapor.
In yet other cases, the overhead stream may also include water vapor because either the feed contains some water or because some steam is injected into the distillation column (which is the case with crude oil distillation towers in petroleum refineries, shown in Figure 4). In those cases, if the overhead distillate product is immiscible in water, the reflux drum may contain a condensed liquid distillate phase, a condensed water phase and a non-condensible gas phase, which makes it necessary that the reflux drum also have a water separation section (as shown in Figure 4).
Plates or trays
Distillation columns (such as in Figures 1 and 2) use various vapor and liquid contacting methods to provide the required number of theoretical equilibrium stages. Such devices are commonly known as "plates" or "trays".[6]
Each of these plates or trays is at a different temperature and pressure. The stage at the tower bottom has the highest pressure and temperature. Progressing upwards in the tower, the pressure and temperature decreases for each succeeding stage. The vapor-liquid equilibrium for each feed component in the tower adjusts to the different pressure and temperature conditions at each of the stages. That means that each component establishes a different concentration in the vapor and liquid phases at each of the stages, and this results in the separation of the components.
Some example trays are depicted in Figure 3. A more detailed, expanded image of two trays can be seen in the theoretical tray article. The reboiler often acts as an additional theoretical equilibrium stage.
If each physical tray or plate were 100% efficient, then the number of physical trays needed for a given separation would equal the number of theoretical equilibrium stages or theoretical plates. However, that is very rarely the case. Hence, a distillation column needs more actual plates than the required number of theoretical vapor-liquid equilibrium stages.
The capacity, pressure drop and efficiency have been experimentally determined for various types of trays used in the distillation of hydrocarbon systems at operating pressures ranging from vacuum to an absolute pressure of 35 bar.[7].
Packed media
Another way of providing for the intimate contacting of vapor and liquid in a distillation column is to use a packing material instead of trays. These offer the advantage of a lower pressure drop across the column (when compared to plates or trays) which is beneficial when operating under vacuum. If a distillation tower uses packing instead of trays, the number of necessary theoretical equilibrium stages is first determined and then the packing height equivalent to a theoretical equilibrium stage, known as the height equivalent to a theoretical plate (HETP), is also determined. The total packing height required is the number theoretical stages multiplied by the HETP.
The packing material can either be random dumped packing such as Raschig rings or structured sheet metal. Liquids tend to wet the surface of the packing and the vapors pass across this wetted surface, where the vapor and liquid contact takes place. Differently shaped packings have different surface areas and void spaces between packings. Both of these factors affect packing performance.
Another factor that affects the performance of random or structured packing is liquid and vapor distribution entering the packed bed. The number of theoretical equilibrium stages required to make a given separation is calculated using a specific vapor to liquid ratio. If the liquid and vapor are not evenly distributed across the superficial tower area as it enters the packed bed, the liquid to vapor ratio will not be correct in the packed bed and the required separation will not be achieved. The problem is not the packing itself but the mal-distribution of the liquid and vapor entering the packed bed. Liquid mal-distribution is more frequently the problem than vapor. The design of the liquid distributors used to introduce the feed and reflux to a packed bed is critical to making the packing perform at maximum efficiency. Methods of evaluating the effectiveness of a liquid distributor can be found in the technical literature.[8][9] Considerable work has also been done on this topic by Fractionation Research, Inc.[10]
Reflux
Virtually all large-scale industrial columns use reflux to achieve a more efficient separation of products.[1][2][3] Reflux refers to the portion of the condensed overhead liquid product from a distillation tower that is returned to the upper part of the tower as shown in Figures 1 and 2. Inside the tower, the downward flowing reflux liquid provides cooling and partial condensation of the upflowing vapors, thereby increasing the efficacy of the distillation tower. The more reflux that is provided, the better is the tower's separation of the lower boiling from the higher boiling components of the feed. The balance of heating with a reboiler at the bottom of a column and cooling by condensed reflux at the top of the column maintains a temperature gradient (or gradual temperature difference) along the height of the column.
Changing the amount of reflux can improve the separation obtained by a continuous distillation column while in operation. This is in contrast to adding plates or trays, or changing the packing, which would at a minimum require a shutdown of operations and a quite significant period of downtime and lost production.
Continuous distillation of crude oil
Petroleum crude oils contain many hundreds of different hydrocarbon compounds: paraffins, naphthenes and aromatics as well as organic sulphur and nitrogen compounds and some oxygen containing hydrocarbons such as phenols. Although crude oils generally do not contain olefins, they are formed in many of the processes used in a petroleum refinery.[11]
The continuous distillation of petroleum crude oil (commonly referred to as crude oil fractionation) is the first processing unit in virtually all petroleum refineries worldwide. It is a somewhat unique example of distillation because it does not produce products having a single boiling point. Instead, it produces fractions having boiling ranges.[11][12]
For example, a crude oil fractionator produces an overhead fraction called naphtha which becomes a gasoline component after it is further processed through a catalytic hydrodesulfurizer to remove sulphur and a catalytic reformer to reform its hydrocarbon molecules into more complex molecules with a higher octane rating value.
The naphtha cut, as that fraction is called, contains many different hydrocarbon compounds. Therefore it has an initial boiling point of about 35 °C and a final boiling point of about 200 °C. Each cut produced in the crude oil fractionator has a different boiling range.
At some distance below the overhead, the next cut is withdrawn from the side of the column and it is usually the jet fuel cut, also known as a kerosene cut. The boiling range of that cut is from an initial boiling point of about 150 °C to a final boiling point of about 270 °C, and it also contains many different hydrocarbons.
The next cut further down the tower is the diesel oil cut with a boiling range from about 180 °C to about 315 °C (not shown in Figure 4 for reasons of brevity). The next cuts down the tower are the light and heavy fuel oil cuts and finally the bottoms product.
The boiling ranges of any two successive cuts overlap because the distillation separations are not perfectly sharp. Typically, all of the cuts from a crude oil fractionator in a petroleum refinery are processed further in subsequent refining processes.
References
- ↑ 1.0 1.1 1.2 Kister, Henry Z. (1992). Distillation Design, 1st Edition. McGraw-Hill. ISBN 0-07-034909-6.
- ↑ 2.0 2.1 King, C.J. (1980). Separation Processes. McGraw Hill. 0-07-034612-7.
- ↑ 3.0 3.1 Perry, Robert H. and Green, Don W. (2007). Perry's Chemical Engineers' Handbook, 8th Edition. McGraw-Hill. ISBN 0-07-142294-3.
- ↑ McCabe, W., Smith, J. and Harriott, P. (2004). Unit Operations of Chemical Engineering, 7th Edition. McGraw Hill. ISBN 0-07-284823-5.
- ↑ R.J. Forbes (1970). A Short History of the Art of Distillation from the Beginnings Up to the Death of Cellier Blumenthal, First Edition (Reprinted). E.J. Brill. ISBN 90-04-00617-6.
- ↑ Photographs of bubble cap and other tray types (Website of Raschig Gmbh)
- ↑ Fractionation Research, Inc. (FRI)
- ↑ Random Packing, Vapor and Liquid Distribution: Liquid and gas distribution in commercial packed towers, Moore, F., Rukovena, F., Chemical Plants & Processing, Edition Europe, August 1987, p. 11-15
- ↑ Structured Packing, Liquid Distribution: A new method to assess liquid distributor quality, Spiegel, L., Chemical Engineering and Processing 45 (2006), p. 1011-1017
- ↑ Packed Tower Distributors: Commercial Scale Experiments That Provide Insight on Packed Tower Distributors, Kunesh, J. G., Lahm, L., Yanagi, T., Ind. Eng. Chem. Res., 1987, vol. 26, p. 1845-1850 Fractionation Research, Inc. (FRI) (Click on "Publications" and then on "K")
- ↑ 11.0 11.1 Gary, J.H. and Handwerk, G.E. (1984). Petroleum Refining Technology and Economics, 2nd Edition. Marcel Dekker, Inc.. ISBN 0-8247-7150-8.
- ↑ Nelson, W.L. (1958). Petroleum Refinery Engineering, 4th Edition. McGraw Hill. LCCN 57010913.