Large-scale trickle filters

Large-scale trickle filters are wastewater treatment facilities for biochemically oxidizing biodegradable substances present in wastewaters. They consist of a fixed bed of rocks, gravel, slag, polyurethane foam or plastic media over which sewage or other biodegradable wastewater percolates downward and is contacted with a layer or film of microbial slime covering the bed media. Aerobic conditions are maintained by air flowing through the bed.[1][2][3][4][5]
The terms trickling biofilter, biofilter, biofilm reactor, biological filter, biological trickling filter and biotower are often used to refer to a trickle filter. These systems have also been described as an attached growth process , a fixed film process, packed media bed filters, roughing filters and percolating filters.
Process mechanism
Referring to Figure 3, the process mechanism involves adsorption of any organic compounds in the sewage or other wastewater by the layer of microbial slime followed by the diffusion of air into the slime layer to furnish the oxygen (O2) required for the biochemical oxidation of the organic compounds that results in releasing gaseous carbon dioxide (CO2), water (H2O) and other oxidized by-products.[1][3][4] The air may be provided by natural draft or by forced aeration using large fans or blowers.
The aerobic biochemical oxidation occurring in a trickle filter may be expressed as:
- Organic compounds + microbes + nutrient + O2 → oxidized organics + CO2 gas + H2O
As the slime layer thickens, it becomes more difficult for air to penetrate the layer and an inner anaerobic layer is formed. For some plastic media , this inner layer will build up and eventually slough off the smooth plastic into the treated effluent water as a sludge that requires subsequent removal and disposal. The sludge consists of dead microbes, non-gaseous oxidized materials, inorganic minerals which are not biodegradable and other substances.
Other than the primary carbon dioxide, water and sludge by-products of the biochemical processes occurring in a trickle filter, there may also be some by-product nitrogen (N2) and methane (CH4) gases.
The following conditions result in the sloughing off of part of the microbial slime layer (referred to as the biofilm) and are intentionally or unintentionally used for control of the biofilm:[1]
- Hydraulic erosion by the continuous flow of water across the surface of the biofilm
- Degradation of the microbes at the interface of the biofilm and surface of the plastic media resulting in a loss of adhesion
- Formation of gases in the biofilm such as carbon dioxide, nitrogen and methane
An ideal filter media is a media that optimizes the surface area for microbial attachment and wastewater retention time, has a high permeability that maximizes air flow, resists plugging and does not degrade.
Configuration of large-scale trickle filters
Figure 4 schematically depicts a typical large-scale trickle filter such as in the photographs shown in Figures 1 and 2. Most large-scale trickle filter systems share the same fundamental components:[5]
- A large containment tank or structure which houses the bed of filter medium
- A filter medium upon which beneficial a beneficial microbial film is promoted and developed
- A distribution method for applying the influent wastewater to the filter medium
- A system, such as a clarifier, for removing the sludge from the treated effluent.
- A pumping system for recycling a portion of the clarified, treated effluent
Each of the arms of the rotating influent water distributor has nozzles that discharge the water in opposite directions, so that the reaction forces of the discharged jets of water cause the distributor to rotate.
Systems can be configured for single-pass use where the influent wastewater is treated in a trickle filter once before being disposed of, or for multi-pass use where a portion of the treated effluent is recycled back to the trickle filter and re-treated. Multi-pass systems result in better effluent quality and assist in reducing the amount of nitrogen-containing compounds by promoting denitrification in the overall system. Nitrogen is one of the principal nutrients found in wastewater and nitrogen-containing discharges into a water resource can severely the resource and it’s associated ecosystem.[5]
Most large-scale trickle filters are used in:
- In municipal wastewater treatment facilities, also referred to as Publicly Owned Treatment Works (PTOW's).
- Onsite within industrial facilities that produce large amounts of biodegradable wastewaters, such as petroleum refineries, petrochemical plants, paper mills and large food processing plants.
Types of large-scale trickle filters
There are a number of different designs for large wastewater trickling filters. Four of the more commonly used designs are:
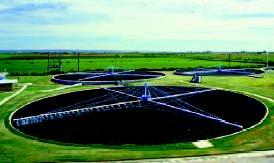
Figure 5: Large, shallow ground-level trickle filters in a municipal wastewater treatment plant[5]
- Above-ground enclosed structures (often called biotowers) as in the photograph shown in Figures 1 and 2 and in the diagram (Figure 4) discussed above: These are used in a good many modern municipal wastewater treatment facilities.
- Shallow, ground-level versions, as in the photograph shown in Figure 5: These are used in many older municipal wastewater treatment plants.
- Vertical packed towers filled with plastic packing[6][7] or other media: As early as the 1960s, such packed towers with plastic media were in use treating industrial wastewaters at: the Pine Bend Petroleum Refinery in Minnesota, U.S.A.; the Trafalgar Refinery in Oakville, Ontario and at a large kraft paper mill.[8] The Pine Bend Refinery tower had a bed consisting of 375 m3 of plastic media, the Trafalgar Refinery had two towers with plastic media beds in each tower that were 6.5 m deep, and the kraft paper mill had 2,750 m3 of plastic media in a 9.5 m deep bed.[8]
- Rotating biological contactors referred to as RBC units: An RBC unit, as depicted in Figure 6, consists of a series of closely spaced, parallel discs mounted on a rotating shaft which is supported just above the surface of the waste water. Microbes grow on the surface of the discs where biological degradation of the wastewater pollutants takes place. The rotating packs of disks (comprised of plastic media) are contained in a trough and rotate at between 2 and 5 revolution per minute. The shaft is aligned with the flow of wastewater so that the discs rotate at right angles to the flow with several packs usually combined to make up a treatment train. About 40% of the disc area is immersed in the wastewater. Aeration is provided by the rotating action, which exposes the media to the air after contacting them with the wastewater. Optionally, forced air flow may be introduced via a distribution pipe in the bottom of the trough.[9][10][11]
References
- ↑ Jump up to: 1.0 1.1 1.2 Duncan Mara and Nigel J. Horan (Editors) (2003). Handbook of Water and Wastewater Microbiology, 1st Edition. Academic Press. ISBN 0-12-470100-0.
- ↑ Marcos Von Sperling (2007). Activated Sludge and Aerobic Biofilm Reactors, 1st Edition. IWA Publishing. ISBN 1-84339-165-1.
- ↑ Jump up to: 3.0 3.1 Paul L. Bishop (2004). Pollution Prevention: Fundamentals and Practice. Waveland Press. ISBN 1-57766-348-9. Lecture on Chapter 11: Residuals Management
- ↑ Jump up to: 4.0 4.1 Milton R. Beychok (1967). Aqueous Wastes from Petroleum and Petrochemical Plants, 1st Edition. John Wiley and Sons. LCCN 67019834.
- ↑ Jump up to: 5.0 5.1 5.2 5.3 Primer for Municipal Wastewater Treatment Systems
- ↑ Biological filter and process U.S. patent 4,351,729, September 28, 1982, Assigned to Celanese Corporation
- ↑ Lecture by Dr. Allen Davis, Auburn University, page 6 of 8 pdf pages including schematic of packed tower trickling filter)
- ↑ Jump up to: 8.0 8.1 E.H. Bryan and D.H. Moeller, Aerobic Biological Oxidation Using Dowpac, Conference on Biological Waste Treatment, Manhattan College, April 1960. Professor Alleman's list of historical papers (Purdue University, Environmental Engineering Department).
- ↑ C.P. Leslie Grady, Glenn T. Daigger and Henry C. Lim (1998). Biological wastewater Treatment, 2nd Edition. CRC Press. ISBN 0-8247-8919-9.
- ↑ C.C. Lee and Shun Dar Lin (2000). Handbook of Environmental Engineering Calculations, 1st Edition. McGraw Hill. ISBN 0-07-038183-6.
- ↑ Tchobanoglous, G., Burton, F.L., and Stensel, H.D. (2003). Wastewater Engineering (Treatment Disposal Reuse) / Metcalf & Eddy, Inc., 4th Edition. McGraw-Hill Book Company. ISBN 0-07-041878-0.
- Pages using ISBN magic links
- CZ Live
- Engineering Workgroup
- Chemistry Workgroup
- Biology Workgroup
- Chemical Engineering Subgroup
- Environmental Engineering Subgroup
- Articles written in American English
- Advanced Articles written in American English
- All Content
- Engineering Content
- Chemistry Content
- Biology Content
- Chemical Engineering tag
- Environmental Engineering tag